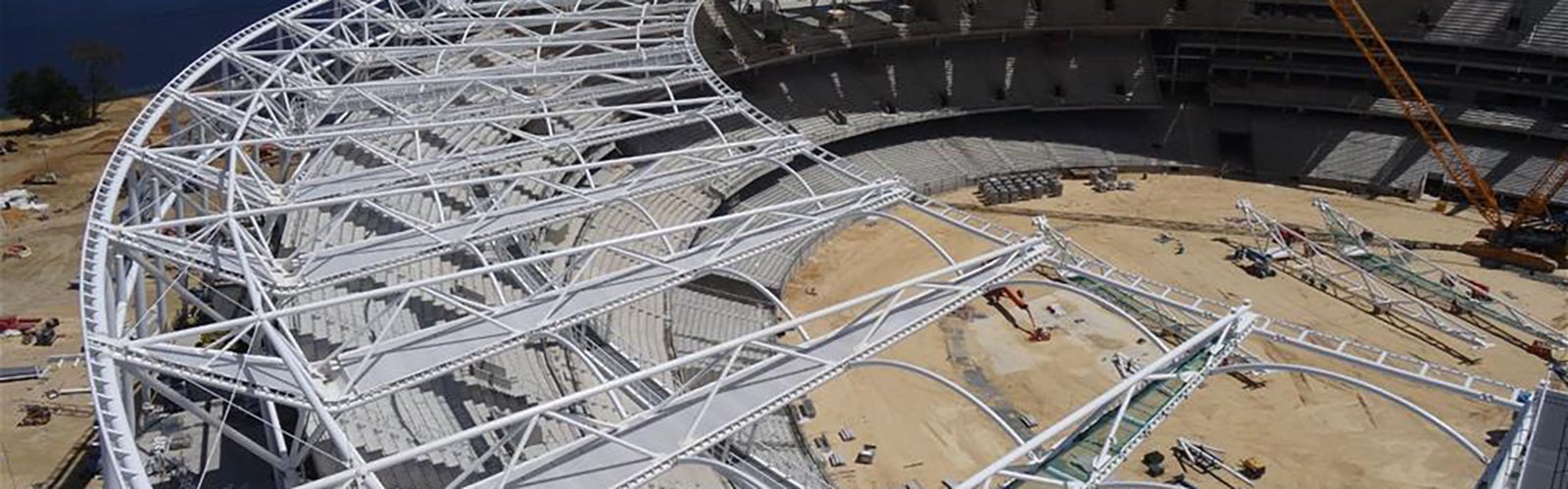
Key Information
- Approximately 16,000 tonnes of welded steel beams, steel plate and large-diameter CHS was supplied by InfraBuild Steel Centre
- InfraBuild Construction Solutions supplied another 13,500 tonnes of reinforcing steel
- The design solution for the roof required removal of concrete structural elements and replacing them with steel V-props
An efficient local supply chain and the forging of several strong relationships have been central to the successful opening of Perth Stadium.
Concert-goers who attended the recent Ed Sheeran show at Perth Stadium have already had a taste of the spectacle offered by the iconic new stadium. And there’s more to come with the much-anticipated opening round of the AFL.
The citizens of Perth have never had it so good. But they can thank a solid supply chain and the forging of several successful partnerships for the stadium meeting its construction targets and opening to the public as scheduled.
Several of the parties involved in the construction of the stadium have attested to the importance of those partnerships in bringing the project together. Construction of the 60,000-seat multipurpose stadium and surrounding Stadium Park began in December 2014, with the stadium meeting each of its milestones in the lead up to its public unveiling.
Approximately 16,000 tonnes of structural steel was supplied by InfraBuild Steel Centre (formerly LIBERTY OneSteel Metalcentre) to construct the five-level stadium superstructure, with another 13,500 tonnes of InfraBuild Construction Solutions (formerly LIBERTY OneSteel Reinforcing) steel also used. A bronze-coloured façade uses anodised aluminium to symbolise Western Australia’s unique geology, while a lightweight fabric roof that covers 85 per cent of seating can be illuminated to display home team colours and graphics.
Supporting local industry
The Perth Stadium project has proved to be a boon for local companies, with over $463.5 million worth of construction contracts awarded to local Western Australian companies throughout the three-year construction phase.
InfraBuild Steel Centre fulfilled the project’s structural steel requirements by engaging with fabricator Civmec to supply 16,000 tonnes of structural steel for the stadium frame, including welded steel beams, steel plate and large-diameter circular hollow sections (CHS). Additional assorted steel materials were supplied to Civmec in the form of hot rolled structural (HRS) sections, merchant bar and tubulars.
The total steel delivered constituted a full supply of the fabricator’s requirements across all the steel product groups and through the use of several different supply chains.
According to InfraBuild Steel Centre Sales Manager Craig Hunter, the relationship between InfraBuild Steel Centre in Perth and Civmec is watertight.
“Since Civmec opened their business, we’ve been their incumbent supplier so the relationship is very strong,” Craig said. “The Perth Stadium project is the smoothest-run I’ve been involved in.”
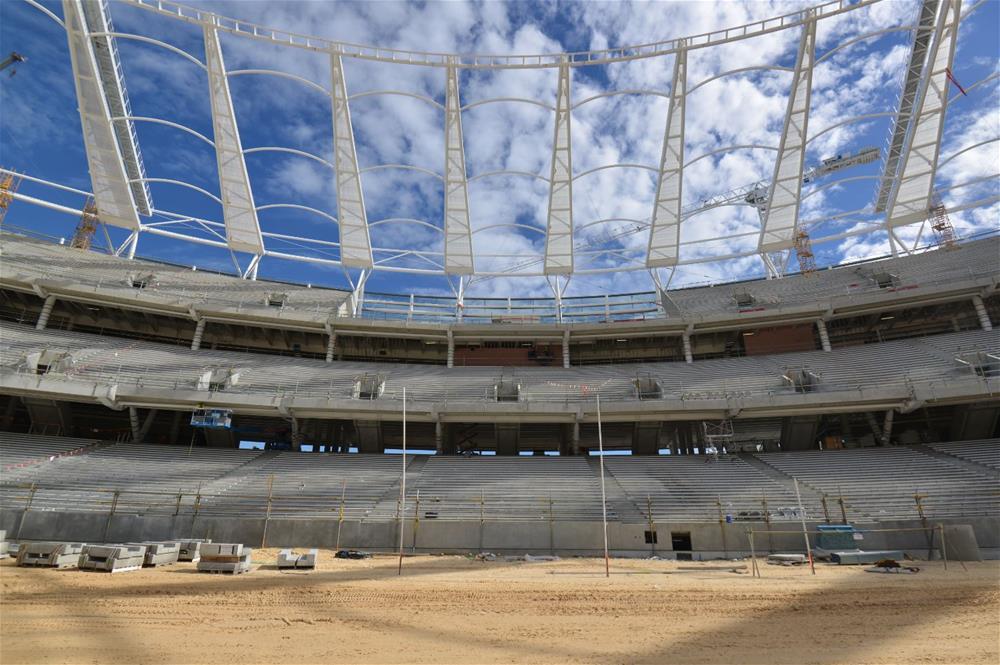
One of the Perth Stadium roof trusses
Craig added InfraBuild Steel Centre offered full traceability and performed independent reviews of all supply chains: “We put them through stringent tests through our national procurement manager, so we were able to ensure the CHS met the Australian Standards.”
Darren Outram, InfraBuild Steel Centre Inventory Manager, added that the company was able to able to provide a significant value-add by ensuring the CHS was ordered to length (thus minimising cutting and waste) and overseeing the removal of weld beads at the mill, which provided a saving in cost and time.
Supply of reinforcing
The Westadium Consortium, which was commissioned to design, build, partially finance and maintain Perth Stadium and Stadium Park, committed early on to supporting the West Australian government’s ‘Building Local Industry’ and ‘Buy Local’ policies. The ASI’s WA State Manager James England worked closely with government to push the value proposition offered by local industry and the importance of engaging trusted local supply chains.
Maurice Murphy, Senior Key Account Manager-Prefabrication and Contracts at InfraBuild Construction Solutions, stated: “We can say, with confidence, that from ground to roof level the majority of the steel used was Australian-made steel.”
With the stadium situated on reclaimed land and requiring approximately 2000 reinforced precast concrete piles to be driven 35m deep in support of the structure, InfraBuild Construction Solutions worked closely with Wagstaff Piling to supply approximately 2500 tonnes of scheduled and precast tolerance processed steel reinforcing bar.
In addition, InfraBuild Construction Solutions Senior Scheduler Dave Carlos was embedded in the project site office, so was able to respond quickly to the needs of on-site engineers in relation to technical queries and supply concerns.
In relation to the pre-cast concrete seating platforms on which the stadium’s spectator seats are mounted, InfraBuild Construction Solutions supplied 1500 tonnes of scheduled and precast tolerance processed steel reinforcing bar to Mundijong-based manufacturer PERMAcast. Over 3000 units make up the stadium seating plats, with over 20,000 tonnes of concrete poured during the manufacturing period.
An additional 10,000 tonnes of scheduled and processed steel reinforcing bar was provided for use in the superstructure.
Steel the solution
Roofing dominates the aesthetics of any stadium design, offering a spectacle to visitors and setting one project apart from another. The design of the Perth Stadium roof, constructed so as to appear as if it is floating above ground, is no different.
The stadium’s design team drew inspiration from the swing arm of a Moto2 World Championship motorcycle for the design of the fifty steel trusses that make up the roof structure.
The structural design solution involved removing the concrete structural elements holding the concrete plates up and replacing them with steel V-props. This allowed the project’s architects to employ consistency of language in relation to the connections and the structure throughout the entire stadium and extending to the roof. Efficient use of steel meant that much of the roof’s material mass could be removed, this delivering significant cost savings.
The project is deserving of every accolade given to it, said InfraBuild Construction Solutions’ Maurice.
“The way the stadium came together is a real credit to the project’s commercial and construction teams, who were outstanding to work with,” he said.
“It is a fabulous-looking stadium and it’s something I know the people of Western Australia are going to be very proud of. The stadium is going to do tremendous things for the state.”
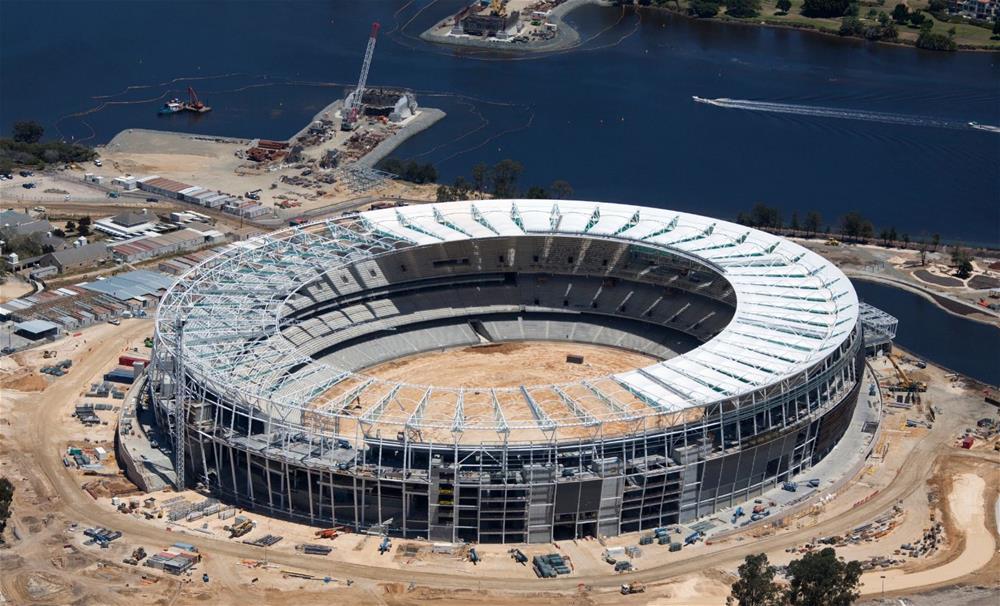
Related Case Studies
Subscribe to the
InfraBuild newsletter
Receive regular updates on news, case studies as well as the latest products and services.