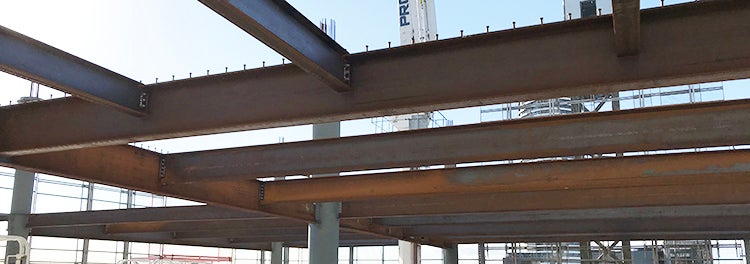
Key Information
- 300 George St: 41-storey 5-star office building of 48,000sqm
- Precambered structural steel supplied by InfraBuild Steel Centre is being used by Beenleigh Steel Fabrications for the Multiplex construction
- Cambered steel sections with pre-set deflection allows lighter sections and reduced floor depth
InfraBuild Steel Centre’s new cambering machine is delivering efficiencies with pre-cambered steel beams for lighter and shallower beams in Brisbane’s latest structural steel high-rise building.
Alongside the 34-storey 5-star W Hotel and 82-storey residential tower The One, the Brisbane Quarter development features a 41-storey commercial tower of 48,342sqm of A-grade office space under construction by Multiplex.
The commercial tower, at 300 George Street in the heart of Brisbane’s CBD, is targeting a 5 Star Green Star rating and is the second recent high-rise development in Brisbane to feature the use of structural steel (after the 480 Queen St development completed in 2016). The new tower is expected to be completed by mid-2019.
Benefits of cambered steel
Two thousand five hundred tonnes of structural steel, made up of hot rolled structural sections (HRS), welded structural sections and structural linepipe, is being supplied to Beenleigh Steel Fabrications by InfraBuild Steel Centre’s (formerly LIBERTY OneSteel Metalcentre) Coopers Plains branch. Seventy per cent of the welded and HRS sections have been supplied cambered. Cambering allows long or heavy load structural sections to have a pre-set deflection added to the beam or column which absorbs load, such as when the slab is poured, and returns to a level and completely horizontal plane.ilding p
The cambered beams deliver significant advantages in allowing the use of lighter beams and smaller sections with less depth than conventional beams. A cambered 530UB92 may be able to be specified in place of a non-cambered 610UB125 or 101, realising a saving over a 10-metre beam of up to 330kg of steel and 70mm of section depth. This can deliver significant benefits in multi-storey constructions including reduced floor depth and weight.
Cambering at Coopers Plains
The cambered structural steel being used for the 300 George Street project is made possible by InfraBuild Steel Centre’s cambering machine at its Coopers Plains branch. The cambering machine has a capacity of up to WB900 structural sections and can induce a camber in an HRS or welded steel section to suit the design criteria for the application. Cambers can be induced into structural sections from 5–200mm if required.

Mick Stoeckert, Construction Manager at Beenleigh Steel Fabrication, says the process is a simple one.
“InfraBuild Steel Centre does all the processing, cutting to length and drilling of all our beams for us,” he says. “Now, with the cambering machine they’re able to supply the beams to us pre-cambered, meaning we don’t need to send them out to a third party.
“It means we’re able to operate to a one-week turnaround instead of two or three.”
The repetitious nature of the project aids the speed of delivery. “Once we got the first few floors out of the way, everyone knows what labour is required to put into it to make the deliveries smoothly,” Mick says. “We take the cambered and processed beams from InfraBuild Steel Centre, add connections as required and then assemble the structure on site.”
Mick believes that the time saving makes a big difference to the pace of the project. “The project is creating a fair bit of interest around the town. Everyone can see that it’s going up a floor a week now. And if the lift core was able to go up quicker, we could be doing two floors a week,” he says.
InfraBuild Steel Centre Coopers Plains’ Peter Davidson says the 300 George Street project has been carefully and successfully managed through load sequencing, with processed steel delivered by InfraBuild Steel Centre level-by-level, some direct to site and some to Beenleigh Steel to be further fabricated.

“The project is utilising the entire processing capability at InfraBuild Steel Centre Coopers Plains including the beamline, coping machine and the cambering machine. This complete processing integration enables a more streamlined and efficient supply chain. We’re able to take significant time, complexity and cost out of the supply chain by offering integrated processing, including pre-cambering, in house. It reduces costs, time required and improves competitiveness,” Peter says.
In addition to the cambering machine in Coopers Plains, InfraBuild Steel Centre has a cambering machine at its Scoresby branch in Melbourne.
Main image courtesy Multiplex.
Related Case Studies
Subscribe to the
InfraBuild newsletter
Receive regular updates on news, case studies as well as the latest products and services.