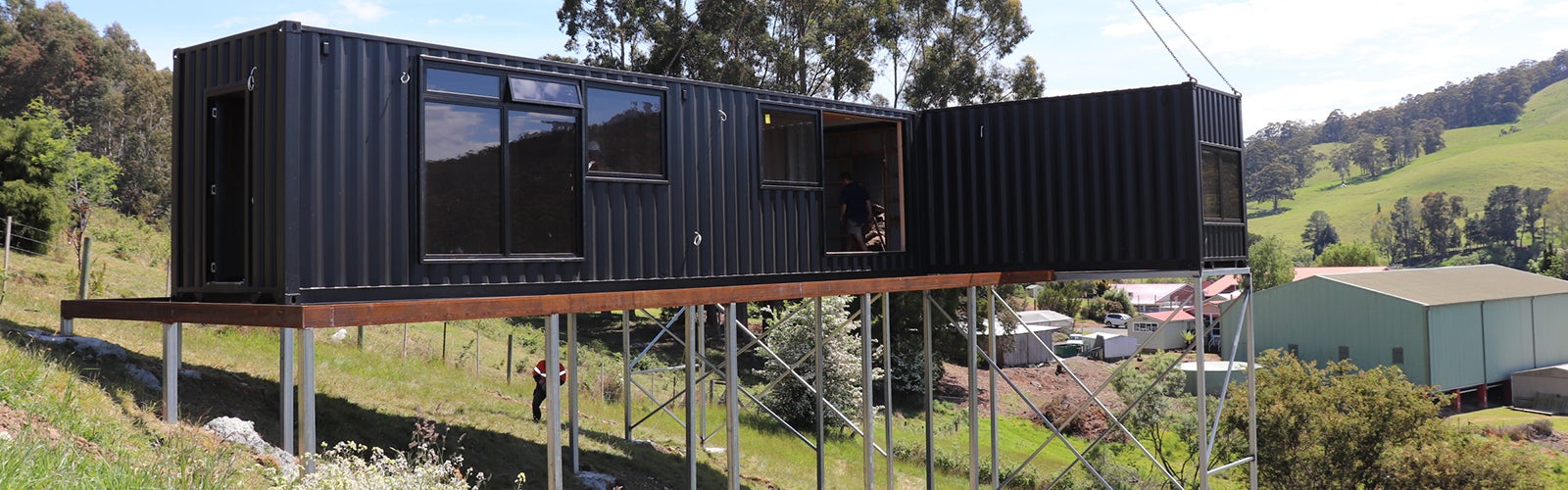
Key Information
All the steelwork required for the supporting frame for this unusual new home was cut to length and supplied by InfraBuild Steel Centre in Tasmania.
It’s not uncommon to find shipping containers taking on new uses once they’ve finished travelling the high seas. But it’s not every day you’ll find two containers welded together and placed on a structural steel support frame to form a house with views over a lush Tasmanian valley.

The images here show just such a structure under construction in Dover, Tasmania, one of Australia’s southernmost towns.
The new dwelling is the brainchild of Matt Stubbs, whose company Containered supplies modular housing solutions to customers looking for up-spec, but affordable, homes that can be transported anywhere in the country.
The Dover house will act as a display home for potential Containered customers to see what housing options are available to them when they consider a modified shipping container home. But it’s also an example of the possibilities offered by structural steel, which has been used throughout the build to transform it into something truly original.
Meeting demand for modular housing
Matt Stubbs says the impetus for his Containered business was spotting a gap in the modular building market.
“You have plenty of people looking for cheap housing in the form of granny flats that can be dropped on site,” he says. “At the other end of the market, you have modular homes available worth $400–500K, which really does defeat the purpose. You may as well buy a house.”
He aims to satisfy the middle ground, by providing affordable, energy efficient and well-appointed modular homes that can be dropped on site even in remote-access areas.

“The beauty of them is they are designed so they can be put on a train or a semi without needing a wide load permit,” Matt says. “It makes them easy to transport and helps keep costs down.”
The Dover home, and the supporting platform on which it has been constructed, has been built by Tasmanian builder Dave Kearney of Kearney Builders. Containered plans on using Kearney Builders as the business expands to meet nationwide demand for the new dwellings.

“Dave Kearney does a great job with these modular homes,” Matt says. “The plan is to expand our operation utilising Kearney Builders to fulfil orders and have the shipping container homes freighted around the country.”
Steel the solution
Three local business used structural steel to create the new home – all of them customers of InfraBuild Steel Centre (formerly LIBERTY OneSteel Metalcentre) Tasmania.
InfraBuild Steel Centre’s Stephen Harvey explains that InfraBuild Steel Centre processed and supplied 100 x 100 x 5.0mm x 8mDuraGal®RHS (rectangular hollow sections) to Kearney Builders for construction of the house’s supporting platform.
“Holes were dug where the columns were to go and then Dave used fabricated gal-dipped casting plates from InfraBuild Steel Centre during the concrete pour,” Stephen explains.
“Surveyors then came in and took measurements for the column heights so we could cut the RHS to size. The RHS was then sent to fabricator Dover Mobile Engineering so they could weld the posts in place on site. The posts were then welded to 50 x 50mm RHS stiffening braces.”
A 15m channel was then delivered to site and installed, after which more 100 x 100 x 5.0mm x 8m DuraGal® RHS was used to construct the frame for the containers to sit on top of.

Duane Cowen from Dover Mobile explains that the 5.5m drop and the uneven ground at the site presented challenges during construction. A telehandler was needed to erect and weld the steelwork and a knuckleboom crane was used to manoeuvre the containers into position for welding to the completed frame.
Container modifications
The shipping containers used in the Dover build were sourced from Melbourne before they were transported to Brighton, Tasmania, for structural modification by container specialist Tassie Containers.

Tassie Containers owner Wayne Silver says his company offers sales and hire of new and used containers, but that container modifications make up a significant part of his business.

“We source various types of RHS and angle from InfraBuild Steel Centre that we use for doors, windows and any large cut-outs that we have to reinforce,” Wayne explains. “The RHS frame gets welded into the container first and then any door or window is then fitted into that RHS.”

After the containers were cut and reinforced, they were delivered to Dave Kearney for a full interior fit-out before transportation to the site at Dover.

The result, says InfraBuild Steel Centre’s Stephen Harvey, is an interesting and unusual project made possible by a reliable and efficient supply of steel and plenty of local know-how.

Related Case Studies
Subscribe to the
InfraBuild newsletter
Receive regular updates on news, case studies as well as the latest products and services.